【動画】MRP利用歴30年!多品種短納期に対応した生産管理[旭モールディング様導入事例]
MRP利用歴30年!多品種短納期に 対応した生産管理
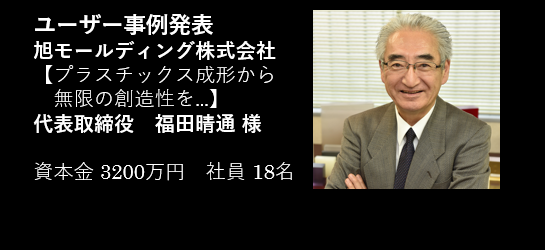
資本金 3200万円 社員 18名。
サイズは小さくても、やるべきことと課題は、大企業と変わらない
限られたスタッフで実践するスピード経営について、お話しいただきました。
MRP利用歴30年の旭モールディング様が、今求める生産管理とは
キーワードは 多品種短納期 です。
------------------------
旭モールディング株式会社代表の福田晴通と申します。
茨城県猿島郡の五霞町というところで射出成型を営んでおります。
全部で18人の小さな会社でございます。資本金は3200万円、年商は4億円程度の会社です。
数十種類の業種の方にまんべんなくプラスチックの製品を供給しているような会社でございます。
実は、1985年に入れたオフィスコンピュータが、NECのエクスプレスサーバ158になります。
今まだOSWindowsMTで動かしています。36年使っています。
そのため代わりのシステムを20年くらいずっと探していたんですよ。
射出成型向きで言いますと、どちらかというと成型機の稼働分析を中心にするシステムですとか、
また生産計画がある程度自動で出来るシステムですとか、色々あるのですけれどもとにかく私どもが
希望するものがない。
特にこれからお話する生産計画をある程度、機敏にやりたいのに、
一歩予定を入れ替えるだけでも希望に沿いませんでした。
例えば、エクセル形式のようなものでドラッグしてシステムに持ってくれば、
予定が変わりますよと紹介されるけれども、変わっていく範囲が全然限定されていたり、
そのあと手動で変えなくてはならないとか、
そのようなシステムばかりに出会っておりまして、本当に困っておりました。
そういう広告ばかり見ていると今度出てくるんですよね、効果って。
ADAPの広告を見てアッと思ったっていうのが入り口でございます。
当社の製造がどういう問題を起こしていたのかを先にお話ししたいと思います。
今のシステムの流れというものどういうものかというと、日々やる随時の業務があります。
工程の調整・生産指示・進捗の管理・在庫管理・進捗管理したりする昼間の時間に
受注データを取り込んでおいて、夕方4時ごろDATのテープでデータを吸い上げまして、
所要量計算をかけます。
そして発注作業に入るという作業を毎日毎日繰り返してます。
そうすると、次のような問題が起きるんですよね。
この問題は、どこの中小企業でもみんな困っているかもしれないんですけれども。
品物を成型→射出成型→印刷→組み立てという流れなんですけれども、
まず工場の方で作る基準予定というものが、昼間のうちに何度もお客様から短納期で
どんどん要求が入って来たりして、一度の夕方の更新だけだともう全然対応ができない・間に合わない。
そのような状況がある中で、日々みんな悶々として対応を取っています。
また、二次工程に回っていった時も各担当の工程が非常に見えにくくて、
個々のエクセルで見えない中で調整していたり、さらにその工程も負荷を自分たちの
経験を中心にしてなんとか均しで収まるように、個々のエクセルで調整していました。
だから私からは何も見えないんですよね。
個々の担当がどこまで何を詰めて、そういう問題を持っているかが見えない。
最終的にはとにかく工程間の在庫も持たないといけない。
この在庫をバッファーとして何とかお客様の納期に間に合わす。
この負荷を均して何とか能力に収まるように抑えてやってきているのが、
現システムのやり方であって大問題でもあります。
これはなぜかというと、受注の状況なんですね。
10年、20年前は、30日以上納期をもらえる注文がほとんどだったんですよ。
ところが今、1か月以上ちゃんと納期をもらっている注文の中に、
リードタイムがないもの・7日から14日の注文がどんどん飛び込んでくる。
そんな短納期の注文が、全体の45%くらい占めているため、
日々調整に大変な思いをしているというのが実情です。
まず、多品種小ロットかつ短納期の注文が飛び込みで入ってくるので、
頻繁な予定変更がかかります。
次に基準予定の作成もままならぬまま、変更と更新が間に合わず、
各担当がマイエクセルで担当工程を調整し、後工程やマイ在庫など現場での調整になってしまう
というスパイラルに本当に困っています。
18人の会社のため、管理しながら現場も掛け持ちなんですよね。
間に合わなければ、現場に入っていって自分も作業を手伝いような状況の中で、
工場長・生産課長・業務課長・品質保証担当者の主に4人くらいが、現システムを回している実情があります。
そのため、担当者が抱えすぎると仕事の精度は落ち、滞り、
納期や在庫などアバウトな回答しかできなくなる。
一番社長として困っているのは、都合の悪いことほど見えないんですよね。
それがある日突然出てくると大問題になるなるようなことがあったりして、
この見える見えない問題というのは、当社にとって本当に大きな問題です。
同時に判断や情報がストップするため、お客様に対する適切なタイミングで
適切な納期回答ができないというのも大きな問題です。
多品種小ロットかつ短納期のニーズで、このような問題を持っていると、
各担当者の負担が大きくて、すごくストレスをかけてしまっているということも大きな問題となっています。
その他、話せないほどいくらでも大変なことがあります。
そんな状況の中で、出会ったのがADAPでした。
十何年働いてきた私の本能で即刻導入しようじゃないかと決めました。
ここで、ADAPに感じた魅力をお伝えします。
ADAPに感じた魅力は計画全体のサプライチェーンを見える化するツールである
ということが明確であることです。
また、各部門が計画に参画して同じ状を見て考えて、コミュニケーションを取りながら
計画遂行を行うという実践的な現場参加型のシステムであることです。
実は、私どもも毎朝関係者を集めてホワイトボードの前で打ち合わせをやっています。
でもそれは今日何をやろうか程度のことしかできないんですよ。
その場で、何がどうなっているというところが分かるような仕組みになっていませんでした。
ADAPでは、ホワイトボードのような仕組みで、何がどうなっているか分かるので、
もう一歩突っ込んだ打合せができると感じました。
そして、計画変更の検討・お客様に対しての納期回答・実績の反映・進捗管理などが、
とにかくすぐに反映されるために、最新の情報を把握することが可能であることです。
先ほどお話した方法以外に、こんな方法があるんだとADAPを知って初めて分かりました。
この手法に感激し、ここまでやらないとやっぱり分からないよねと思いました。
次にADAPに期待することです。
まず何といっても見える化です。各担当者がどうなっているのか全然見えなかったので、
その進捗・工程・在庫切れ・発注点のタイミング・工程の負荷が見えることで、
前もって手を打てるようになると非常に感じております。
そしてスピードですよね、即時更新できるということ。日時更新を待たずに瞬時に見れる。
さらに各個人による管理をやる必要がない。
正しい情報が、判断がより速い進むことによって仕事の精度が上がるとすごく感じております。
あとお客様に対する納期回答率の向上、原価改善と経営改善、ここら辺が大きなポイントになっています。
そして一番は従業員の現場の負担感ですね。そしてそこから来るやる気にも
影響しあうことをやってあげれば、またやる気が出てきて頑張ってくれるんじゃないかなと期待しています。
最後にADAPを導入することで、どのくらいの数値の効果があるかを少し算出してみました。
今、計画しているのは、仕掛在庫の圧縮と製品在庫の圧縮を、5年間で約1700万。
さらに、製品の売上生産計画がスムーズになることによりまして、
売上高の特に粗利益の増加額を約1100万円見ております。
労務費の効果、残業代や休日出勤の減少を計算してみますと、
約500万円の削減を見込んでおります。
社員一同、この数値目標を達成しようと話し合っております。